Lean to filozofia, której założenia można wdrożyć w organizacjach o różnym profilu działalności – zarówno tych niewielkich, jak i bardzo rozbudowanych. Szczególnie dobrze sprawdza się w zakładach produkcyjnych oraz przedsiębiorstwach, w których istotną częścią działalności jest magazynowanie. Co warto wiedzieć o lean management i jak założenia tej koncepcji wyglądają w praktyce?
Koncepcja lean – krótka historia
Koncepcja lean powstała w Japonii, w zakładach produkcyjnych marki Toyota. Była rozwijana od lat 40. i 50. XX wieku pod nazwą TPS – Toyota Production System. Samo pojęcie lean production (szczupła produkcja) zostało sformułowane pod koniec lat 80.
Współcześnie lean management jest szeroką i do pewnego stopnia uniwersalną dziedziną, którą adaptuje się w organizacjach o różnych profilach działalności. Najszerzej stosuje się ją tam, gdzie miała swoje początki – w branżach produkcyjnych i tych związanych z magazynowaniem.
Przeczytaj także: Czym jest strefa niebezpieczna i jak ją wydzielić?
Główne założenia filozofii lean
Lean jest zbiorem założeń, które pozwalają optymalizować pracę przedsiębiorstwa, przede wszystkim przez modyfikację (porządkowanie) kluczowych procesów, szeroko rozumianą standaryzację, a także wyeliminowanie czynności, które zajmują dużo czasu, a jednocześnie są nieefektywne (lub też przynoszą niewielkie rezultaty względem poniesionych nakładów).
Nieustanne dążenie do eliminowania marnotrawstwa jest bardzo ważnym elementem strategii lean. Produkcja „odchudzona” z marnowania zasobów jest produkcją najbardziej efektywną. Obszary, na których skupia się koncepcja, to przede wszystkim:
- ujednolicenie procedur, standaryzacja
- usprawnienie powtarzalnych procesów,
- uproszczenie zbyt skomplikowanych ścieżek pracy (jeśli możliwe),
- przepływ i dostępność informacji, decyzyjność.
Lean management w produkcji – od czego zacząć?
Pierwszym krokiem do wprowadzenia zasad lean w zakładzie jest analiza obecnej sytuacji: wskazanie czynników, które sprawiają, że procesy są nieefektywne i przyczyniają się do powstawania strat. Narzędzia, które mogą w tym pomóc, to na przykład:
- Analiza SWOT – szczegółowe zestawienie mocnych stron, słabych stron, szans i zagrożeń.
- Mapowanie strumienia wartości – graficzne zestawienie ważnych procesów, przepływu komunikacji i innych zdarzeń, które mają miejsce w firmie (i na tej podstawie zaplanowanie nowych, funkcjonalnych przepływów).
Określenie wartości, jakimi kieruje się przedsiębiorstwo, jest bardzo ważne, ponieważ to na tej podstawie wybiera się cele, do których należy dążyć oraz elementy będące marnotrawstwem (które przeszkadzają w realizacji tych celów).
Lean w produkcji – jak wygląda w praktyce?
Proces modernizacji przedsiębiorstwa powinien być możliwie szeroki, tzn. należy zaangażować w niego pracowników wszystkich działów, łącznie z kadrą zarządzającą. Stosuje się także decentralizację, szczególnie w procesach decyzyjnych – eliminując kolejne instancje zatwierdzania, można zaoszczędzić relatywnie dużo czasu. Wdrożenie nowych zasad powinno być także poprzedzone przygotowaniem pracowników – szkoleniami, dostosowaniem miejsc pracy do nowych warunków.
W kontekście zespołu ważne jest wzbudzanie poczucia, że konkretne stanowisko pracy jest istotne dla całościowo rozumianego procesu produkcji. W lean manufacturing stosuje się na przykład zasadę TPM (Total Productive Maintenance), która polega na zaangażowaniu pracowników w proces utrzymania jakości maszyn, co pomaga ograniczać przestoje i awarie. Z kolei zasada SMED (Single Minute Exchange of Die) to wymiana narzędzi/przezbrojenie w bardzo krótkim czasie, ograniczonym do jednocyfrowej liczby minut.
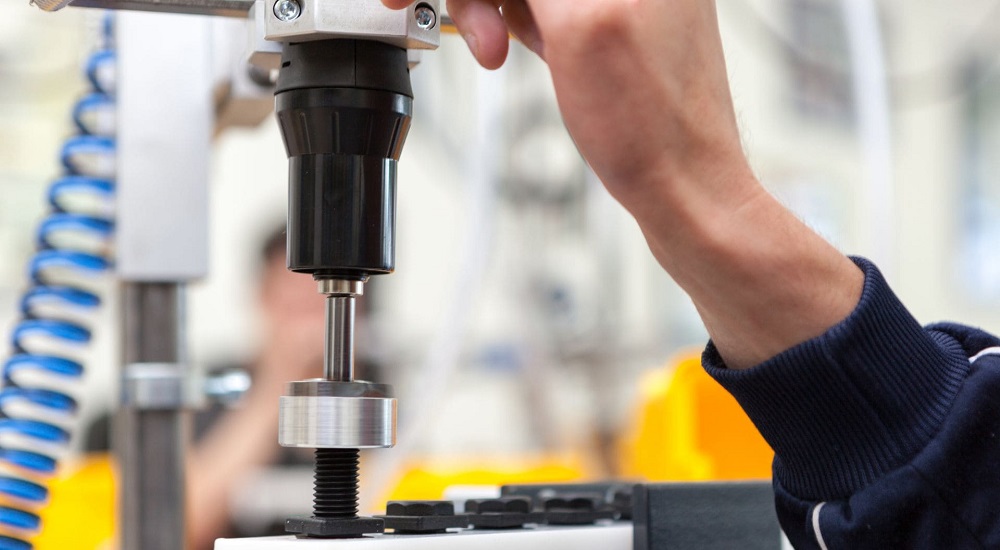
Lean w magazynie i produkcji – przykłady technik
Lean management w magazynie można wdrożyć z wykorzystaniem wielu różnych technik i rozwiązań. Przykładem dwóch, które stosowano w zakładach Toyoty, to:
- Dostawy dokładnie na czas (system just in time). Wytworzenie systemu ssącego, zamiast pchanego (wyciąganego), charakterystycznego dla tradycyjnej produkcji. W systemie ssącym wytwarza się dokładnie tyle półproduktów na danym etapie, ile będzie potrzebne w kolejnym. Nie wytwarza się ich mniej, by pracownicy nie musieli czekać i nie więcej, by uniknąć magazynowania. To z kolei ogranicza marnotrawstwo, ponieważ zakład otrzymuje tylko te materiały, na które jest obecnie zapotrzebowanie.
- Autonomizacja (jidoka) – „automatyzacja z ludzką inteligencją”, czyli takie zaprojektowanie procesów, które pozwoli pracownikom wykrywanie i eliminowanie błędów – wszelkich odstępstw od przyjętych standardów. Dotyczy to każdego etapu powstawania produktu, dlatego ważne jest, by w proces zaangażować pracowników wszystkich szczebli. Pracownik linii produkcyjnej ma prawo zatrzymać proces, jeśli zauważy błąd, który może w krótkim czasie naprawić bez angażowania większej liczby osób.
Najważniejszą zasadą lean jest zatem ciągły przepływ produkcji (prowadzenie jej w płynny sposób), a unikanie produkcji w dużych partiach, która zwykle prowadzi do nadmiernego magazynowania.
Przykłady lean w magazynie
Aby ograniczyć ilość składowanych zapasów, stosuje się strategię cross-docking, tzn. przekazywanie dostarczonego towaru do klienta bez jego magazynowania. Dzięki temu klient otrzymuje zamówienie szybciej, a organizacja nie ponosi kosztów związanych z przechowywaniem towarów (przez co rozumiemy również czas i zaangażowanie pracowników). Istotne jest również skrócenie samego czasu dostawy. Wymaga to skoordynowania procesów zachodzących na produkcji, w dziale zaopatrzenia, sprzedaży oraz logistyce.
W koncepcji lean ważną rolę odgrywa też standaryzacja przestrzeni (np. dzięki metodzie 5S) i stosowanie odpowiednich oznaczeń – pomocne mogą być w tym tablice, oznaczenia dróg komunikacyjnych, czy miejsc składowania towarów.
Sprawdź przykładowe tablice lean, które warto zastosować w magazynie oraz dodatkowe akcesoria do tablic lean.
Dlaczego warto wdrożyć zasady lean w przedsiębiorstwie?
Szczupła produkcja wiąże się z bardzo wyraźnym zmniejszeniem:
- czasu poświęconego na procesy produkcyjne,
- liczby pracowników niezbędnych do wykonywania zadań,
- ilości magazynowanych materiałów,
- przestrzeni niezbędnej do wykonywania zadań,
- usterek maszyn, zatorów lub konieczności poprawiania poszczególnych elementów procesu.
Dobrze zarządzany proces to korzyści zarówno dla organizacji, jak i jej klientów. Zakład produkuje szybciej, mniejszym nakładem czasu i kosztów, z ograniczeniem awarii i przestojów. Zwiększa się również zadowolenie pracowników na wszystkich szczeblach, a organizacja działa sprawniej. Z kolei jej klienci otrzymują towary wysokiej jakości, możliwie szybko. Optymalizacja produkcji pozwala też oferować konkurencyjne ceny, co jest szansą na zdobycie nowych odbiorców.